Describe some of the extraction methods and identify different types of mining.
In order to use the resources at our disposal, we need to be able to get to them. This section introduces the different techniques used to extract or remove these resources.
What You’ll Learn to Do
- Describe the processes involved in mining.
- Identify the effects of different types of mining: surface mining, underground mining and open pit mining.
Mining
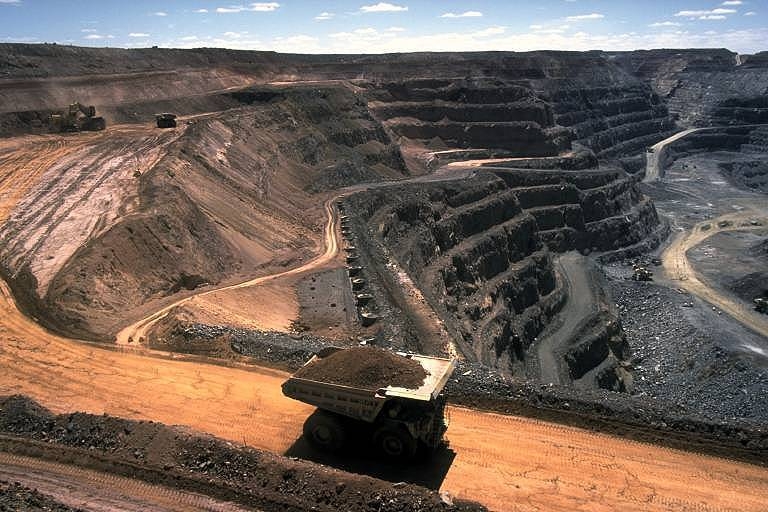
Figure 1. Surface coal mining
Mining is the extraction of valuable minerals or other geological materials from the earth from an orebody, lode, vein, seam, or reef, which forms the mineralized package of economic interest to the miner.
Ores recovered by mining include metals, coal, oil shale, gemstones, limestone, dimension stone, rock salt, potash, gravel, and clay. Mining is required to obtain any material that cannot be grown through agricultural processes, or created artificially in a laboratory or factory. Mining in a wider sense includes extraction of any non-renewable resource such as petroleum, natural gas, or even water.
Mining of stone and metal has been done since pre-historic times. Modern mining processes involve prospecting for ore bodies, analysis of the profit potential of a proposed mine, extraction of the desired materials, and final reclamation of the land after the mine is closed.
The nature of mining processes creates a potential negative impact on the environment both during the mining operations and for years after the mine is closed. This impact has led most of the world’s nations to adopt regulations designed to moderate the negative effects of mining operations. Safety has long been a concern as well, and modern practices have improved safety in mines significantly.
Mining Techniques
Mining techniques can be divided into two common excavation types: surface mining and sub-surface (underground) mining. Today, surface mining is much more common, and produces, for example, 85% of minerals (excluding petroleum and natural gas) in the United States, including 98% of metallic ores.
Targets are divided into two general categories of materials: placer deposits, consisting of valuable minerals contained within river gravels, beach sands, and other unconsolidated materials; and lode deposits, where valuable minerals are found in veins, in layers, or in mineral grains generally distributed throughout a mass of actual rock. Both types of ore deposit, placer or lode, are mined by both surface and underground methods.
Some mining, including much of the rare earth elements and uranium mining, is done by less-common methods, such as in-situ leaching: this technique involves digging neither at the surface nor underground. The extraction of target minerals by this technique requires that they be soluble, e.g., potash, potassium chloride, sodium chloride, sodium sulfate, which dissolve in water. Some minerals, such as copper minerals and uranium oxide, require acid or carbonate solutions to dissolve.
Surface Mining
Surface mining is done by removing (stripping) surface vegetation, dirt, and, if necessary, layers of bedrock in order to reach buried ore deposits.

Figure 2. Garzweiler surface mine, Germany
Open-pit mining, or open-cast mining is a surface mining technique of extracting rock or minerals from the earth by their removal from an open pit or borrow.
This form of mining differs from extractive methods that require tunneling into the earth, such as long wall mining. Open-pit mines are used when deposits of commercially useful minerals or rocks are found near the surface; that is, where the overburden (surface material covering the valuable deposit) is relatively thin or the material of interest is structurally unsuitable for tunneling (as would be the case for sand, cinder, and gravel). For minerals that occur deep below the surface—where the overburden is thick or the mineral occurs as veins in hard rock—underground mining methods extract the valued material.
Open-pit mines that produce building materials and dimension stone are commonly referred to as “quarries.”
Open-pit mines are typically enlarged until either the mineral resource is exhausted, or an increasing ratio of overburden to ore makes further mining uneconomic. When this occurs, the exhausted mines are sometimes converted to landfills for disposal of solid wastes. However, some form of water control is usually required to keep the mine pit from becoming a lake, if the mine is situated in a climate of considerable precipitation or if any layers of the pit forming the mine border productive aquifers.

Figure 3. Note the angled and stepped sides of the Sunrise Dam Gold Mine, Australia.
Open-cast mines are dug on benches, which describe vertical levels of the hole. These benches are usually on four to sixty meter intervals, depending on the size of the machinery that is being used. Many quarries do not use benches, as they are usually shallow.
Most walls of the pit are generally dug on an angle less than vertical, to prevent and minimize damage and danger from rock falls. This depends on how weathered the rocks are, and the type of rock, and also how many structural weaknesses occur within the rocks, such as a faults, shears, joints orfoliations.
The walls are stepped. De-watering bores may be used to relieve water pressure by drilling horizontally into the wall, which is often enough to cause failures in the wall by itself.
Waste rock is piled up at the surface, near the edge of the open pit. This is known as the waste dump. The waste dump is also tiered and stepped, to minimize degradation.
Ore which has been processed is known as tailings, and is generally a slurry. This is pumped to a tailings dam or settling pond, where the water evaporates. Tailings dams can often be toxic due to the presence of unextracted sulfide minerals, some forms of toxic minerals in the gangue, and often cyanide which is used to treat gold ore via the cyanide leach process. This toxicity can harm the surrounding environment.
Gold is generally extracted in open-pit mines at 1 to 2 ppm (parts per million); but with certain techniques (e.g. bulk leaching) and with high gold values much lower levels can be economic.
Materials typically extracted from open-pit mines include:
- Bitumen
- Clay
- Coal
- Copper
- Coquina
- Diamonds
- Gravel and stone (stone refers to bedrock, while gravel is unconsolidated material)
- Granite
- Gritstone
- Gypsum
- Limestone
- Marble
- Metal ores, such as Copper, Iron, Gold, Silver and Molybdenum
- Uranium
- Phosphate
Underground Mining

Figure 4. Mantrip used for transporting miners within an underground mine
Sub-surface mining consists of digging tunnels or shafts into the earth to reach buried ore deposits. Ore, for processing, and waste rock, for disposal, are brought to the surface through the tunnels and shafts.
Machines
Heavy machinery is used in mining to explore and develop sites, to remove and stockpile overburden, to break and remove rocks of various hardness and toughness, to process the ore, and to carry out reclamation projects after the mine is closed. Bulldozers, drills, explosives and trucks are all necessary for excavating the land. In the case of placer mining, unconsolidated gravel, or alluvium, is fed into machinery consisting of a hopper and a shaking screen or trommel which frees the desired minerals from the waste gravel. The minerals are then concentrated using sluices or jigs.
Large drills are used to sink shafts, excavate stopes, and obtain samples for analysis. Trams are used to transport miners, minerals and waste. Lifts carry miners into and out of mines, and move rock and ore out, and machinery in and out, of underground mines. Huge trucks, shovels and cranes are employed in surface mining to move large quantities of overburden and ore. Processing plants utilize large crushers, mills, reactors, roasters and other equipment to consolidate the mineral-rich material and extract the desired compounds and metals from the ore.

Figure 5. The Bagger 288 is a bucket-wheel excavator used in strip mining. It is also the largest land vehicle of all time.
Processing
Once the mineral is extracted, it is often then processed. The science of extractive metallurgy is a specialized area in the science of metallurgy that studies the extraction of valuable metals from their ores, especially through chemical or mechanical means.
Mineral processing (or mineral dressing) is a specialized area in the science of metallurgy that studies the mechanical means of crushing, grinding, and washing that enable the separation (extractive metallurgy) of valuable metals or minerals from their gangue (waste material). Processing of placer ore material consists of gravity-dependent methods of separation, such as sluice boxes. Only minor shaking or washing may be necessary to disaggregate (unclump) the sands or gravels before processing. Processing of ore from a lode mine, whether it is a surface or subsurface mine, requires that the rock ore be crushed and pulverized before extraction of the valuable minerals begins. After lode ore is crushed, recovery of the valuable minerals is done by one, or a combination of several, mechanical and chemical techniques.
Since most metals are present in ores as oxides or sulfides, the metal needs to be reduced to its metallic form. This can be accomplished through chemical means such as smelting or through electrolytic reduction, as in the case of aluminium. Geometallurgy combines the geologic sciences with extractive metallurgy and mining.
Mining Industry
Mining exists in many countries. London is known as the capital of global “mining houses” such as Rio Tinto Group, BHP Billiton, and Anglo American PLC. The US mining industry is also large, but it is dominated by the coal and other nonmetal minerals (e.g., rock and sand), and various regulations have worked to reduce the significance of mining in the United States. In 2007 the totalmarket capitalization of mining companies was reported at US$962 billion, which compares to a total global market cap of publicly traded companies of about US$50 trillion in 2007. In 2002, Chile and Peru were reportedly the major mining countries of South America. The mineral industry of Africa includes the mining of various minerals; it produces relatively little of the industrial metals copper, lead, and zinc, but according to one estimate has as a percent of world reserves 40% of gold, 60% of cobalt, and 90% of the world’s platinum group metals. Mining in India is a significant part of that country’s economy. In the developed world, mining in Australia, with BHP Billiton founded and headquartered in the country, and mining in Canada are particularly significant. For rare earth minerals mining, China reportedly controlled 95% of production in 2013.
Mining operations can be grouped into five major categories in terms of their respective resources. These are oil and gas extraction, coal mining, metal ore mining, nonmetallic mineral mining and quarrying, and mining support activities. Of all of these categories, oil and gas extraction remains one of the largest in terms of its global economic importance. Prospecting potential mining sites, a vital area of concern for the mining industry, is now done using sophisticated new technologies such as seismic prospecting and remote-sensing satellites. Mining is heavily affected by the prices of the commodity minerals, which are often volatile. The 2000s commodities boom (“commodities supercycle”) increased the prices of commodities, driving aggressive mining. In addition, the price of gold increased dramatically in the 2000s, which increased gold mining; for example, one study found that conversion of forest in the Amazon increased six-fold from the period 2003–2006 (292 ha/yr) to the period 2006–2009 (1,915 ha/yr), largely due to artisanal mining.
Safety
Safety has long been a concern in the mining business especially in sub-surface mining. The Courrières mine disaster, Europe’s worst mining accident, involved the death of 1,099 miners in Northern France on March 10, 1906. This disaster was surpassed only by the Benxihu Colliery accident in China on April 26, 1942, which killed 1,549 miners. While mining today is substantially safer than it was in previous decades, mining accidents still occur. Government figures indicate that 5,000 Chinese miners die in accidents each year, while other reports have suggested a figure as high as 20,000. Mining accidents continue worldwide, including accidents causing dozens of fatalities at a time such as the 2007 Ulyanovskaya Mine disaster in Russia, the 2009 Heilongjiang mine explosion in China, and the 2010 Upper Big Branch Mine disaster in the United States.
Mining ventilation is a significant safety concern for many miners.
Gases in mines can poison the workers or displace the oxygen in the mine, causing asphyxiation.
Ignited methane gas is a common source of explosions in coal mines, which in turn can initiate more extensive coal dust explosions.
Miners utilize equipment strong enough to break through extremely hard layers of the Earth’s crust. This equipment, combined with the closed work space in which underground miners work, can cause hearing loss. For example, a roof bolter (commonly used by mine roof bolter operators) can reach sound power levels of up to 115 dB. Combined with the reverberant effects of underground mines, a miner without proper hearing protection is at a high risk forhearing loss. By age 50, nearly 90% of U.S. coal miners have some hearing loss, compared to only 10% among workers not exposed to loud noises.
Since mining entails removing dirt and rock from its natural location, thereby creating large empty pits, rooms, and tunnels, cave-ins as well as ground and rock falls are a major concern within mines. Modern techniques for timbering and bracing walls and ceilings within sub-surface mines have reduced the number of fatalities due to cave-ins, but ground falls continue to represent up to 50% of mining fatalities. Even in cases where mine collapses are not instantly fatal, they can trap mine workers deep underground. Cases such as these often lead to high-profile rescue efforts, such as when 33 Chilean miners were trapped deep underground for 69 days in 2010.
High temperatures and humidity may result in heat-related illnesses, including heat stroke, which can be fatal.
Effects of Mining
Environmental Effects
Environmental issues can include erosion, formation of sinkholes, loss of biodiversity, and contamination of soil, groundwater and surface water by chemicals from mining processes. In some cases, additional forest logging is done in the vicinity of mines to create space for the storage of the created debris and soil. Contamination resulting from leakage of chemicals can also affect the health of the local population if not properly controlled. Extreme examples of pollution from mining activities include coal fires, which can last for years or even decades, producing massive amounts of environmental damage.
Mining companies in most countries are required to follow stringent environmental and rehabilitation codes in order to minimize environmental impact and avoid impacting human health. These codes and regulations all require the common steps of environmental impact assessment, development of environmental management plans, mine closure planning (which must be done before the start of mining operations), and environmental monitoring during operation and after closure. However, in some areas, particularly in the developing world, government regulations may not be well enforced.
Waste
Ore mills generate large amounts of waste, called tailings. For example, 99 tons of waste are generated per ton of copper, with even higher ratios in gold mining. These tailings can be toxic. Tailings, which are usually produced as a slurry, are most commonly dumped into ponds made from naturally existing valleys. These ponds are secured by impoundments (dams or embankment dams). In 2000 it was estimated that 3,500 tailings impoundments existed, and that every year, 2 to 5 major failures and 35 minor failures occurred; for example, in the Marcopper mining disaster at least 2 million tons of tailings were released into a local river. Subaqueous tailings disposal is another option. The mining industry has argued that submarine tailings disposal (STD), which disposes of tailings in the sea, is ideal because it avoids the risks of tailings ponds; although the practice is illegal in the United States and Canada, it is used in the developing world.
The waste is classified as either sterile or mineralised, with acid generating potential, and the movement and storage of this material forms a major part of the mine planning process. When the mineralised package is determined by an economic cut-off, the near-grade mineralised waste is usually dumped separately with view to later treatment should market conditions change and it becomes economically viable. Civil engineering design parameters are used in the design of the waste dumps, and special conditions apply to high-rainfall areas and to seismically active areas. Waste dump designs must meet all regulatory requirements of the country in whose jurisdiction the mine is located. It is also common practice to rehabilitate dumps to an internationally acceptable standard, which in some cases means that higher standards than the local regulatory standard are applied.
Open-Pit Mining

Figure 6. Opencut coal mine loadout station and reclaimed land at the North Antelope Rochelle coal mine in Wyoming, United States.
After mining finishes, the mine area must undergo rehabilitation. Waste dumps are contoured to flatten them out, to further stabilise them. If the ore contains sulfides it is usually covered with a layer of clay to prevent access of rain and oxygen from the air, which can oxidise the sulfides to produce sulfuric acid, a phenomenon known as acid mine drainage. This is then generally covered with soil, and vegetation is planted to help consolidate the material. Eventually this layer will erode, but it is generally hoped that the rate of leaching or acid will be slowed by the cover such that the environment can handle the load of acid and associated heavy metals. There are no long term studies on the success of these covers due to the relatively short time in which large scale open pit mining has existed. It may take hundreds to thousands of years for some waste dumps to become “acid neutral” and stop leaching to the environment. The dumps are usually fenced off to prevent livestock denuding them of vegetation. The open pit is then surrounded with afence, to prevent access, and it generally eventually fills up with ground water. In arid areas it may not fill due to deep groundwater levels.

Figure 7. An open-pit sulfur mine at Tarnobrzeg, Poland undergoing land rehabilitation
Metal Reserves and Recycling
During the twentieth century, the variety of metals used in society grew rapidly. Today, the development of major nations such as China and India and advances in technologies are fueling an ever greater demand. The result is that metal mining activities are expanding and more and more of the world’s metal stocks are above ground in use rather than below ground as unused reserves. An example is the in-use stock of copper. Between 1932 and 1999, copper in use in the USA rose from 73 kilograms (161 lb) to 238 kilograms (525 lb) per person.
95% of the energy used to make aluminum from bauxite ore is saved by using recycled material. However, levels of metals recycling are generally low. In 2010, the International Resource Panel, hosted by the United Nations Environment Programme (UNEP), published reports on metal stocks that exist within society and their recycling rates.
The report’s authors observed that the metal stocks in society can serve as huge mines above ground. However, they warned that the recycling rates of some rare metals used in applications such as mobile phones, battery packs for hybrid cars, and fuel cells are so low that unless future end-of-life recycling rates are dramatically stepped up these critical metals will become unavailable for use in modern technology.
Candela Citations
- Introduction to Extraction of Resources. Authored by: Kimberly Schulte and Lumen Learning. Provided by: Lumen Learning. License: CC BY: Attribution
- Revision and adaptation of Wikipedia content. Authored by: Kimberly Schulte and Lumen Learning. Provided by: Lumen Learning. License: CC BY-SA: Attribution-ShareAlike
- Mining. Provided by: Wikipedia. Located at: http://en.wikipedia.org/wiki/Mining. License: CC BY-SA: Attribution-ShareAlike
- Open-pit mining. Provided by: Wikipedia. Located at: http://en.wikipedia.org/wiki/Open-pit_mining. License: CC BY-SA: Attribution-ShareAlike