What you’ll learn to do: explain the basic control process and monitoring points
Controlling activities and behaviors is a dynamic process, a cycle of repeated corrections. The steps in the control process will be repeated in the course of production activities. The categories of control, based on the perspective of time, include feedback, concurrent, and proactive controls. These use past and present information or future projections to improve an activity. Managers use all of these controls to manage their business.
Learning Outcomes
- Explain the basic control process.
- Differentiate between feedback, proactive, and concurrent controls.
The proper performance of the management control function is critical to the success of an organization. After plans are set in place, management must execute a series of steps to ensure that the plans are carried out. The steps in the basic control process can be followed for almost any application, such as improving product quality, reducing waste, and increasing sales. The basic control process includes the following steps:
- Setting performance standards: Managers must translate plans into performance standards. These performance standards can be in the form of goals, such as revenue from sales over a period of time. The standards should be attainable, measurable, and clear.
- Measuring actual performance: If performance is not measured, it cannot be ascertained whether standards have been met.
- Comparing actual performance with standards or goals: Accept or reject the product or outcome.
- Analyzing deviations: Managers must determine why standards were not met. This step also involves determining whether more control is necessary or if the standard should be changed.
- Taking corrective action: After the reasons for deviations have been determined, managers can then develop solutions for issues with meeting the standards and make changes to processes or behaviors.
Consider a situation in which a fictional company, The XYZ Group, has suffered a decrease in the profits from its high-end sunglasses due to employee theft. Senior executives establish a plan to eliminate the occurrence of employee theft. It has been determined that the items are being stolen from the company warehouse. The executives establish a goal of zero thefts ($0) within a three-month period (Step 1). The company currently loses an average of $1,000 per month due to employee theft.
To discourage the undesired behavior, XYZ installed cameras in the warehouse and placed locks on the cabinets where the most expensive sunglasses are stored. Only the warehouse managers have keys to these cabinets.
After three months, XYZ managers contact the bookkeeper to get the sales and inventory figures for the past three-month period (Step 2). The managers then compare the figures with the previous period, taking into account orders for deliveries, returns, and defective merchandise (Step 3). It has been determined that the company lost $200 the first month, $300 the second month, and $200 the third month due to theft, which is an improvement but short of the goal. Managers then come up with suggestions for making adjustments to the control system (Step 4).
XYZ senior executives approve of the suggestion to institute a zero-tolerance policy for employee theft. Now, if there is evidence that an employee has stolen a pair of sunglasses, that employee’s job will be terminated. The employee handbook is updated to include the change, and XYZ executives hold a meeting with all warehouse employees to communicate the policy change (Step 5).
Timing of Controls
Controls can be categorized according to the time in which a process or activity occurs. The controls related to time include feedback, proactive, and concurrent controls. Feedback control concerns the past. Proactive control anticipates future implications. Concurrent control concerns the present.
Feedback
Feedback occurs after an activity or process is completed. It is reactive. For example, feedback control would involve evaluating a team’s progress by comparing the production standard to the actual production output. If the standard or goal is met, production continues. If not, adjustments can be made to the process or to the standard.
An example of feedback control is when a sales goal is set, the sales team works to reach that goal for three months, and at the end of the three-month period, managers review the results and determine whether the sales goal was achieved. As part of the process, managers may also implement changes if the goal is not achieved. Three months after the changes are implemented, managers will review the new results to see whether the goal was achieved.
The disadvantage of feedback control is that modifications can be made only after a process has already been completed or an action has taken place. A situation may have ended before managers are aware of any issues. Therefore, feedback control is more suited for processes, behaviors, or events that are repeated over time, rather than those that are not repeated.
Proactive control
Proactive control, also known as preliminary, preventive, or feed-forward control, involves anticipating trouble, rather than waiting for a poor outcome and reacting afterward. It is about prevention or intervention. An example of proactive control is when an engineer performs tests on the braking system of a prototype vehicle before the vehicle design is moved on to be mass produced.
Proactive control looks forward to problems that could reasonably occur and devises methods to prevent the problems. It cannot control unforeseen and unlikely incidents, such as “acts of God.”
Concurrent control
With concurrent control, monitoring takes place during the process or activity. Concurrent control may be based on standards, rules, codes, and policies.
One example of concurrent control is fleet tracking. Fleet tracking by GPS allows managers to monitor company vehicles. Managers can determine when vehicles reach their destinations and the speed in which they move between destinations. Managers are able to plan more efficient routes and alert drivers to change routes to avoid heavy traffic. It also discourages employees from running personal errands during work hours.
In another example, Keen Media tries to reduce employee inefficiency by monitoring Internet activity. In accordance with company policy, employees keep a digital record of their activities during the workday. IT staff can also access employee computers to determine how much time is being spent on the Internet to conduct personal business and “surf the Web.”
The following diagram shows the control process. Note that the production process is central, and the control process surrounds it.
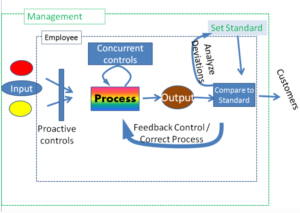
The control process
Check Your Understanding
Answer the question(s) below to see how well you understand the topics covered in the previous section. This short quiz does not count toward your grade in the class, and you can retake it an unlimited number of times.
Use this quiz to check your understanding and decide whether to (1) study the previous section further or (2) move on to the next section.
Candela Citations
- The Control Process. Authored by: Talia Lambarki and Lumen Learning. License: CC BY: Attribution
- Image: The Control Process. Authored by: Robert Carroll and Lumen Learning. License: CC BY: Attribution