Learning Objectives
In this module, the following topics are covered: 1) combined heat and power (CHP) as an alternative energy source, 2) CHP component characteristics and operational benefits, 3) the characteristics of good CHP applications.
After reading this module, students should be able to
- define combined heat and power (CHP) as an alternative energy source
- provide CHP component characteristics and operational benefits
- outline the characteristics of good CHP applications
Introduction
Electricity in the United States is generated, for the most part, from central station power plants at a conversion efficiency of roughly 30 to 35 percent. Meaning, for every 100 units of fuel energy into a simple cycle central station electric power plant, we get only 30 to 35 units of electricity. The remainder of the energy in the fuel is lost to the atmosphere in the form of heat.
The thermal requirements of our buildings and facilities are generally provided on-site through the use of a boiler or furnace. The efficiencies of this equipment have improved over the years and now it is common to have boilers and furnaces in commercial and industrial facilities with efficiencies of 80 percent and higher. Meaning, for every 100 units of fuel energy into the boiler/furnace, we get about 80 units of useful thermal energy.
Commercial and industrial facilities that utilize the conventional energy system found in the United States (electricity supplied from the electric grid and thermal energy produced on-site through the use of a boiler/furnace) will often times experience overall fuel efficiencies of between 40 to 55 percent (actual efficiency depends on the facilities heat to power ratio).
Combined Heat and Power (CHP) is a form of distributed generation. It is an integrated system located at or near the building/facility that generates utility grade electricity which satisfies at least a portion of the electrical load of the facility, and captures and recycles the waste heat from the electric generating equipment to provide useful thermal energy to the facility.
Conventional CHP (also referred to as topping cycle CHP) utilizes a single dedicated fuel source to sequentially produce useful electric and thermal power. Figure Conventional (Topping Cycle) CHP provides a diagram of a typical topping cycle CHP system. A variety of fossil fuels, renewable fuels, and waste products are utilized as input fuel to power a prime mover that generates mechanical shaft power (exception is fuel cells). Prime movers might include reciprocating engines, gas turbines, steam turbines or fuel cells. The mechanical shaft power is converted into utility grade electricity through a highly efficient generator. Since the CHP system is located at or near the building/facility, the heat lost through the prime mover can be recycled through a heat exchanger and provide heating, cooling (absorption chillers), and/or dehumidification (desiccants) to meet the thermal load of the building. These systems can reach fuel use efficiencies of as high as 75 to 85 percent (versus the conventional energy system at approximately 40 to 55 percent).
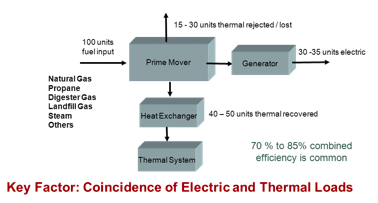
Conventional (Topping Cycle) CHP Diagram illustrates a typical topping cycle of CHP systems. Source: John Cuttica
In our example of 100 units of fuel into the CHP system, only 30 to 35 units of electricity are generated, but another 40 to 50 units of the fuels energy can be recovered and utilized to produce thermal power. What this tells us is that for conventional CHP systems to reach the high efficiency level, there must be a use for the recovered thermal energy. Thus a key factor for conventional CHP systems is the coincidence of electric and thermal loads in the building. This is shown in Figure Importance of Waste Heat Recovery. The “Y” axis represents the cost of generating electricity with a CHP system utilizing a 32 percent efficient reciprocating engine. The “X” axis represents the cost of natural gas utilized to operate the CHP system and also the value of the natural gas being displaced if the recycled heat from the engine can be utilized. The lines in the chart show various levels of recoverable heat available from the engine. If no heat is recovered (no use for the thermal energy), the cost of generating electricity with the CHP system is $0.08/kWhr. When the full amount of heat from the engine is recovered (full use of the thermal energy), the cost of generating electricity with the CHP system then drops to $0.03/kWhr.
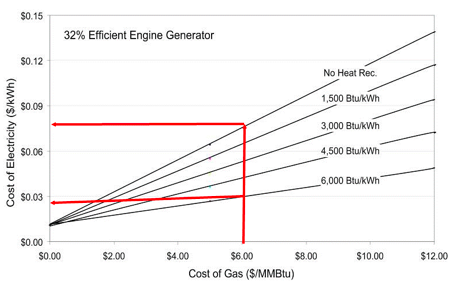
Importance of Waste Heat Recovery Graph shows the importance of waste heat recovery in CHP systems. Source: John Cuttica
Since the high efficiency of a CHP system is dependent on the effective use of the recoverable heat, CHP systems are often times sized to meet the thermal load of the application and the amount of electricity produced is the by-product. The electricity is used to off set the electricity otherwise purchased from the local electric utility. When the CHP system does not produce enough electricity to satisfy the load, the utility supplies the difference from the grid. When the CHP system (sized from the thermal requirements) produces more electricity than the load requires, the excess electricity can be sold to the local utility (normally at the avoided cost of power to the utility).
There are three general modes of operation for CHP on-site generators relative to the electric utility grid:
- Stand Alone (totally isolated from the grid)
- Isolated from the grid with utility back-up (when needed)
- Parallel operation with the grid
The preferred mode of operation is parallel with the grid. Both the on-site CHP system and the utility grid power the facility simultaneously. With a proper sizing and configuration of the CHP system, the parallel mode of operation provides the most flexibility. Should the grid go down, the CHP system can keep operating (e.g. during the 2003 Northeast Blackout and the 2005 Hurricane Katrina), and should the CHP system go down, the utility grid can supply power to the load. Overall reliability of power to the load is increased.
The basic components of a conventional (topping cycle) CHP system are:
- Prime Mover that generates mechanical shaft energy
- Reciprocating engine
- Turbines (gas, micro, steam)
- Fuel Cell (fuel cells ustilize an electrochemical process rather than a mechanical shaft process)
- Generator converts the mechanical shaft energy into electrical energy
- Synchronous generator (provides most flexibility and independence from the grid)
- Induction generator (grid goes down – the CHP system stops operating)
- Inverter (used mainly on fuel cells – converts DC power to utility grade AC power)
- Waste Heat Recovery is one or more heat exchangers that capture and recycle the heat from the prime mover
- Thermal Utilization equipment converts the recycled heat into useful heating, cooling (absorption chillers) and/or dehumidification (deisiccant dehumidifiers)
- Operating Control Systems insure the CHP components function properly together
Reducing CO2 Emissions
In 2007, McKinsey & Company published a study on reducing United States greenhouse gas emissions. The report analyzed the cost and potential impact of over 250 technology options regarding contribution to reducing CO2 emissions. Two conclusions stated in the report were:
- Abatement opportunities are highly fragmented and spread across the economy.
- Almost 40 percent of abatement could be achieved at negative marginal costs.
Figure Cost of CO2 Reduction Technologies emphasizes both of these points. It is interesting to point out that CHP (both industrial and commercial applications), when sized and installed appropriately, delivers CO2 reductions at a negative marginal cost. All the technologies that show a negative marginal cost on the chart generate positive economic returns over the technology’s life cycle. The figure also shows that in terms of cost effectiveness of the wide range of abatement technologies, energy efficiency measures are by far more effective than renewable, nuclear and clean coal generating technologies. CHP technologies stand out as having negative marginal costs and overall positive cost effectiveness comparable to most of the energy efficiency measures.
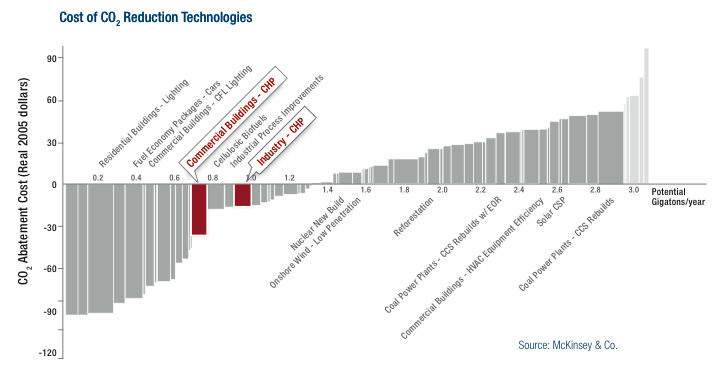
Cost of CO2 Reduction Technologies Figure shows the cost of CO2 reduction technologies. Source: Oak Ridge National Laboratory (2008), p. 13, and McKinsey & Company, “Reducing U.S. Greenhouse Gas Emissions: How Much at What Cost?,” December, 2007
CHP Applications
Today there are more than 3,500 CHP installations in the United States, totaling more than 85,000 MW of electric generation. That represents approximately 9 percent of the total electric generation capacity in the United States. The 85,000 MW of installed CHP reduces energy consumption by 1.9 Quads (1015 Btus) annually and eliminates approximately 248 million metric tons (MMT) of CO2 annually.
CHP systems are generally more attractive for applications that have one or more of the following characteristics:
- Good coincidence between electric and thermal loads
- Maximum cost differential between electricity cost from the local utility and the cost of the fuel utilized in the CHP system (referred to as spark spread)
- Long operating hours (normally more than 3,000 hours annually)
- Need for good power quality and reliability
The following are just a few of the type applications where CHP makes sense:
- Hospitals
- Colleges and Universities
- High Schools
- Fitness Centers
- Office Buildings
- Hotels
- Data Centers
- Prisons
- Pulp and Paper Mills
- Chemical Manufacturing Plants
- Metal Fabrication Facilities
- Glass Manufacturers
- Ethanol Plants
- Food Processing Plants
- Waste Water Treatment Facilities
- Livestock Farms
CHP Benefits
CHP is not the only solution to our energy problems. In fact, CHP is not the most cost effective solution in all applications or in all areas of the country. There are many variables that determine the viability of CHP installations. However, when the technical and financial requirements of the application are met, a well designed, installed and operated CHP system provides benefits for the facility owner (end user), the electric utility, and society in general. The high efficiency attained by the CHP system provides the end user with lower overall energy costs, improved electric reliability, improved electric power quality, and improved energy security. In areas where the electric utility distribution grid is in need of expansion and/or upgrades, CHP systems can provide the electric utility with a means of deferring costly modifications to the grid. Although the electricity generated on-site by the end user displaces the electricity purchased from the local electric utility and is seen as lost revenue by many utilities, energy efficiency and lower utility costs are in the best interest of the utility customer and should be considered as a reasonable customer option by forward-looking customer oriented utilities. Finally, society in general benefits from the high efficiencies realized by CHP systems. The high efficiencies translate to less air pollutants (lower greenhouse gas and NOx emissions) than produced from central station electric power plants.
Waste Heat to Power
There is a second type of CHP system, referred to as Waste Heat to Power (Bottoming Cycle CHP). Unlike conventional CHP where a dedicated fuel is combusted in a prime mover, Waste Heat to Power CHP systems captures the heat otherwise wasted in an industrial or commercial process. The waste heat, rather than the process fuel, becomes the fuel source for the waste heat to power system. It is used to generate steam or hot water, which in turn is utilized to drive a steam turbine or (for lower temperatures) an organic rankine cycle heat engine. In this case, the waste heat from the industrial/commercial process is converted to electric power. Figure Waste Heat to Power (Bottoming Cycle) CHP provides a diagram of a Waste Heat to Power CHP system.
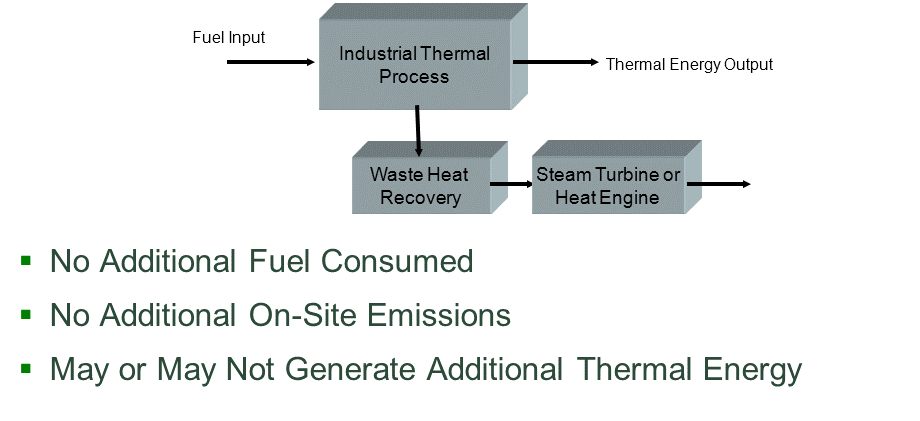
Waste Heat to Power (Bottoming Cycle) CHP Diagram illustrates a waste heat to power (bottoming cycle) CHP system. Source: John Cuttica
Summary
Combined Heat and Power (CHP) represents a proven and effective near-term alternative energy option that can enhance energy efficiency, ensure environmental quality, and promote economic growth. The concept of generating electricity on-site allows one to capture and recycle the waste heat from the prime mover providing fuel use efficiencies as high as 75 to 85 percent. Like other forms of alternative energy, CHP should be considered and included in any portfolio of energy options.
Review Questions
What drives the system efficiency in a conventional CHP system?
To ensure high system efficiency, how would you size a conventional CHP system?
What is the preferred method of operating a CHP system that provides the most flexibility with the utility grid?
Why are CHP systems considered one of the most cost-effective CO2 abatement practices?
Name at least three application characteristics that make CHP an attractive choice.
Resources
For more information on Combined Heat and Power and Waste Heat to Power, see www.midwestcleanenergy.org
References
Oak Ridge National Laboratory. (2008). Combined Heat and Power, Effective Energy Solutions for a Sustainable Future. Retrieved September 26, 2011 from http://www1.eere.energy.gov/industry/distributedenergy/pdfs/chp_report_12-08.pdf
Glossary
- Absorption Chiller
- Utilizes heat instead of mechanical energy to provide cooling. A thermal compressor (fueled by the waste heat from the CHP system) is used in place of an electrically powered mechanical compressor in the refrigeration process.
- Avoided Cost of Power
- The marginal cost for a utility to produce one more unit of power.
- Combined Heat and Power (CHP)
- An integrated system, located at or near the building or facility, that generates utility grade electricity which satisfies at least a portion of the electrical load of the facility and captures/ recycles the waste heat from the electric generating equipment to provide useful thermal energy to the facility.
- Conventional CHP (Topping Cycle CHP)
- Utilizes a single dedicated fuel source to sequentially produce useful electric and thermal power.
- Desiccant Dehumidification
- Process that removes moisture (latent load) from a building air stream by passing the air over a desiccant wheel (normally a silica gel). The recovered heat from a CHP system is utilized to regenerate the desiccant by driving the moisture off the desiccant wheel to the outside.
- Fuel Cell
- An exothermic electrochemical reaction that combines hydrogen and oxygen ions through an electrolyte material to generate electricity (DC) and heat.
- Gas Turbine
- An internal-combustion engine consisting essentially of an air compressor, combustion chamber, and turbine wheel that is turned by the expanding products of combustion.
- Induction Generator
- Converts the mechanical shaft power from the CHP prime mover to utility grade Alternating Current Power. An induction generator can only operate when connected to an external reactive power source (normally provided by the utility grid).
- Inverter
- Converts Direct Current electric power into utility grade Alternating Current electric power. Normally used with fuel cell systems.
- Organic Rankine Cycle (ORC)
- Uses an organic, high molecular mass fluid with a liquid-vapor phase change or boiling point occurring at a lower temperature than the water-steam phase change. The fluid allows rankine cycle heat recovery from lower temperature sources where the heat is converted into useful work, which can then be converted into electricity.
- Prime Mover
- The term utilized to denote the CHP system equipment that converts input fuel into mechanical shaft power (reciprocating engine, gas turbine, steam turbine, micro-turbine).
- Reciprocating Engine
- A heat engine that uses one or more reciprocating pistons to convert pressure into mechanical rotating shaft power.
- Steam Turbine
- Utilizes the Rankine Cycle to extract heat from steam and transform the heat into mechanical shaft power by expanding the steam from high pressure to low pressure through the turbine blades.
- Synchronous Generator
- Converts the mechanical shaft power from the CHP prime mover to utility grade Alternating Current Power. A synchronous generator is self-exciting (contains its own source of reactive power) and can operate independent of, or isolated from, the utility grid.
- Waste Heat to Power (Bottoming Cycle CHP)
- Captures the waste heat generated by an industrial or commercial process, utilizing the waste heat as the free fuel source for generating electricity.
Candela Citations
- Sustainability: A Comprehensive Foundation. Authored by: Tom Theis and Jonathan Tomkin, Editors.. Provided by: OpenStax CNX. Located at: http://cnx.org/contents/1741effd-9cda-4b2b-a91e-003e6f587263@44.1. License: CC BY: Attribution. License Terms: Download for free at http://cnx.org/contents/1741effd-9cda-4b2b-a91e-003e6f587263@44.1