25.6: Social Change
25.6.1: The Factory System
The factory system, fueled by technological progress, made production much faster, cheaper, and more uniform, but also disconnected the workers from the means of production and placed them under the control of powerful industrialists.
Learning Objective
Describe the factory system and how it functioned
Key Points
- One of the earliest factories was John Lombe’s water-powered silk mill at Derby, operational by 1721. By 1746, an integrated brass mill was working at Warmley near Bristol. Matthew Boulton at his Soho Manufactory, which started operating in 1766, was among the pioneers of mass production on the assembly line principle, while Josiah Wedgwood in Staffordshire opened the first true ceramics factory in 1769.
- The factory system began to grow rapidly when cotton spinning was mechanized. Richard Arkwright, the founder of the first successful cotton spinning factory in the world, is credited with inventing the prototype of the modern factory. Other industrialists and industries followed, introducing novel practices that advanced the factory system, including mass production using interchangeable parts or modern materials such as cranes and rail tracks through the buildings for handling heavy items.
- The major characteristics of factory system are that is a capitalist form of production, where the labor does not own a significant share of the enterprise; the capitalist owners provide the means of production and are responsible for the sale; production relies on unskilled labor; products are produced on a much larger scale than in either the putting-out or crafts systems; the location of production is more flexible; precisely uniform components are produced thanks to machinery; workers are paid either daily wages or for piece work, either in the form of money or a combination of money, goods, and services.
- The factory system was a new way of organizing labor made necessary by the development of machines, which were too large to house in a worker’s cottage. Working hours were as long as they had been for the farmer: from dawn to dusk, six days per week. Factories also essentially reduced skilled and unskilled workers to replaceable commodities. Debate arose concerning the morality of the factory system, as workers complained about unfair working conditions.
- The transition to industrialization was not without difficulty. For example, a group of English textile workers known as Luddites protested against industrialization and sometimes sabotaged factories. They feared that the years workers spent learning a craft would go to waste and unskilled machine operators would rob them of their livelihood. However, in many industries the transition to factory production was not so divisive.
- One of the best-known accounts of factory worker’s living conditions during the Industrial Revolution is Friedrich Engels’ The Condition of the Working Class in England in 1844. Since then, the historical debate on the question of living conditions of factory workers has been very controversial. While some have pointed out that industrialization slowly improved the living standards of workers, others have concluded that living standards for the majority of the population did not grow meaningfully until much later.
Key Terms
- Luddites
- A group of English textile workers and self-employed weavers in the 19th century that used the destruction of machinery as a form of protest. The group was protesting the use of machinery in a “fraudulent and deceitful manner” to get around standard labor practices. They were fearful that the years they spent learning the craft would go to waste and unskilled machine operators would rob them of their livelihoods.
- putting-out system
- A means of subcontracting work, historically known also as the workshop system and the domestic system. Work is contracted by a central agent to subcontractors who complete the work in off-site facilities, either in their own homes or in workshops with multiple craftsmen.
- factory system
- A method of manufacturing using machinery and division of labor, first adopted in Britain at the beginning of the Industrial Revolution in the late 18th century and later spread around the world. Use of machinery with the division of labor reduced the required skill level of workers and increased the output per worker.
- truck system
- An arrangement in which employees are paid in commodities or some currency substitute (such as vouchers or token coins, called in some dialects scrip or chit) rather than with standard currency.
Growth of Factories
One of the earliest factories was John Lombe’s water-powered silk mill at Derby, operational by 1721. By 1746, an integrated brass mill was working at Warmley near Bristol. Raw material went in at one end, was smelted into brass, then turned into pans, pins, wire, and other goods. Housing was provided for workers on site. Matthew Boulton at his Soho Manufactory, which started operating in 1766, was among the pioneers of mass production on the assembly line principle while Josiah Wedgwood in Staffordshire opened the first true ceramics factory in 1769.
The factory system began to grow rapidly when cotton spinning was mechanized. Richard Arkwright, the founder of the first successful cotton spinning factory in the world, is credited with inventing the prototype of the modern factory. After he patented his water frame in 1769, he established Cromford Mill in Derbyshire, England, significantly expanding the village of Cromford to accommodate the migrant workers new to the area. Mass production using interchangeable parts was first achieved in 1803 by Marc Isambard Brunel in cooperation with Henry Maudslay and Simon Goodrich, for the British Royal Navy during the Napoleonic War. This method did not catch on in general manufacturing in Britain for many decades; when it did, it was imported from the United States, becoming known as the American system of manufacturing. The Nasmyth, Gaskell and Company’s Bridgewater Foundry, which began operation in 1836, was one of the earliest factories to use modern materials handling, such as cranes and rail tracks through the buildings for heavy items.
Between 1820 and 1850, mechanized factories supplanted traditional artisan shops as the predominant form of manufacturing institution, because the larger-scale factories enjoyed a significant technological advantage over the small artisan shops. The earliest factories under the factory system developed in the cotton and wool textiles industry. Later generations of factories included mechanized shoe production and manufacturing of machinery, including machine tools. Factories that supplied the railroad industry included rolling mills, foundries, and locomotive works. Agricultural-equipment factories produced cast-steel plows and reapers. Bicycles were mass-produced beginning in the 1880s.
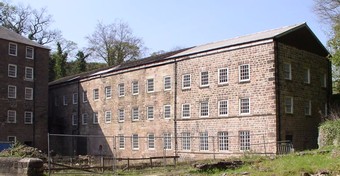
The Cromford Mill (opened in 1771) today: Richard Arkwright is the person credited with inventing the prototype of the modern factory. After he patented his water frame in 1769, he established Cromford Mill, in Derbyshire, England, significantly expanding the village of Cromford to accommodate the migrant workers new to the area. It laid the foundation of Arkwright’s fortune and was quickly copied by mills in Lancashire, Germany and the United States.
Characteristics of Factory System
The factory system, considered a capitalist form of production, differs dramatically from the earlier systems of production. First, the labor generally does not own a significant share of the enterprise. The capitalist owners provide all machinery, buildings, management and administration, and raw or semi-finished materials, and are responsible for the sale of all production as well as any resulting losses. The cost and complexity of machinery, especially that powered by water or steam, was more than cottage industry workers could afford or had the skills to maintain. Second, production relies on unskilled labor. Before the factory system, skilled craftsmen would usually custom-made an entire article. In contrast, factories practiced division of labor, in which most workers were either lowskilled laborers who tended or operated machinery, or unskilled laborers who moved materials and semi-finished and finished goods. Third, factories produced products on a much larger scale than in either the putting-out or crafts systems.
The factory system also made the location of production much more flexible. Before the widespread use of steam engines and railroads, most factories were located at water power sites and near water transportation. When railroads became widespread, factories could be located away from water power sites but nearer railroads. Workers and machines were brought together in a central factory complex. Although the earliest factories were usually all under one roof, different operations were sometimes on different floors. Further, machinery made it possible to produce precisely uniform components.
Workers were paid either daily wages or for piece work, either in the form of money or some combination of money, housing, meals, and goods from a company store (the truck system). Piece work presented accounting difficulties, especially as volumes increased and workers did a narrower scope of work on each piece. Piece work went out of favor with the advent of the production line, which was designed on standard times for each operation in the sequence and workers had to keep up with the work flow.
Factory System and Society
The factory system was a new way of organizing labor made necessary by the development of machines, which were too large to house in a worker’s cottage. Working hours were as long as they had been for the farmer: from dawn to dusk, six days per week. Factories also essentially reduced skilled and unskilled workers to replaceable commodities. At the farm or in the cottage industry, each family member and worker was indispensable to a given operation and workers had to posses knowledge and often advanced skills that resulted from years of learning through practice. Conversely, under the factory system, workers were easily replaceable as skills required to operate machines could be acquired very quickly. Factory workers typically lived within walking distance to work until the introduction of bicycles and electric street railways in the 1890s. Thus, the factory system was partly responsible for the rise of urban living, as large numbers of workers migrated into the towns in search of employment in the factories. Many mills had to provide dormitories for workers, especially for girls and women.
Much manufacturing in the 18th century was carried out in homes under the domestic or putting-out system, especially the weaving of cloth and spinning of thread and yarn, often with just a single loom or spinning wheel. As these devices were mechanized, machine-made goods were able to underprice the cottagers, leaving them unable to earn enough to make their efforts worthwhile.
The transition to industrialization was not without difficulty. For example, a group of English textile workers known as Luddites protested against industrialization and sometimes sabotaged factories. They continued an already established tradition of workers opposing labor-saving machinery. Numerous inventors in the textile industry suffered harassment when developing their machines or devices. Despite the common stereotype of Luddites as opponent of progress, the group was in fact protesting the use of machinery in a “fraudulent and deceitful manner” to get around standard labor practices. They feared that the years workers had spent learning a craft would go to waste and unskilled machine operators would rob them of their livelihoods. However, in many industries the transition to factory production was not so divisive.
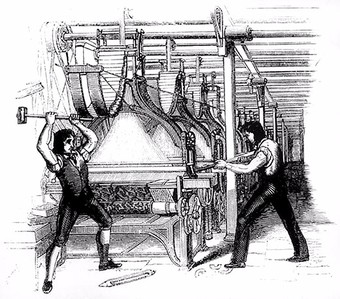
Frame-breakers, or Luddites, smashing a loom
Machine-breaking was criminalized by the Parliament of the United Kingdom as early as 1721. Parliament subsequently made “machine breaking” (i.e. industrial sabotage) a capital crime with the Frame Breaking Act of 1812 and the Malicious Damage Act of 1861. Lord Byron opposed this legislation, becoming one of the few prominent defenders of the Luddites.
Debate arose concerning the morality of the factory system, as workers complained about unfair working conditions. One of the problems concerned women’s labor. Women were always paid less than men and in many cases, as little as a quarter of what men made. Child labor was also a major part of the system. However, in the early 19th century, education was not compulsory and in working families, children’s wages were seen as a necessary contribution to the family budget. Automation in the late 19th century is credited with ending child labor and according to many historians, it was more effective than gradually changing child labor laws. Years of schooling began to increase sharply from the end of the 19th century, when elementary state-provided education for all became a viable concept (with the Prussian and Austrian empires as pioneers of obligatory education laws). Some industrialists themselves tried to improve factory and living conditions for their workers. One of the earliest such reformers was Robert Owen, known for his pioneering efforts in improving conditions for workers at the New Lanark mills and often regarded as one of the key thinkers of the early socialist movement.
One of the best-known accounts of factory worker’s living conditions during the Industrial Revolution is Friedrich Engels’ The Condition of the Working Class in England in 1844. In it, Engels described backstreet sections of Manchester and other mill towns where people lived in crude shanties and shacks, some not completely enclosed, some with dirt floors. These shanty towns had narrow walkways between irregularly shaped lots and dwellings. There were no sanitary facilities. Population density was extremely high. Eight to ten unrelated mill workers often shared a room with no furniture and slept on a pile of straw or sawdust. Disease spread through a contaminated water supply. By the late 1880s, Engels noted that the extreme poverty and lack of sanitation he wrote about in 1844 had largely disappeared. Since then, the historical debate on the question of living conditions of factory workers has been very controversial. While some have pointed out that living conditions of the poor workers were tragic everywhere and industrialization, in fact, slowly improved the living standards of a steadily increasing number of workers, others have concluded that living standards for the majority of the population did not grow meaningfully until the late 19th and 20th centuries and that in many ways workers’ living standards declined under early capitalism.
Attributions
- The Factory System
-
“FrameBreaking-1812.jpg.” https://commons.wikimedia.org/wiki/File:FrameBreaking-1812.jpg. Wikimedia Commons Public domain.
-
“Cromford_1771_mill.jpg.” https://commons.wikimedia.org/wiki/File:Cromford_1771_mill.jpg. Wikimedia Commons Public domain.
Candela Citations
- Boundless World History. Authored by: Boundless. Located at: https://courses.lumenlearning.com/boundless-worldhistory/. License: CC BY: Attribution