Learning Outcomes
- Explain the flow of costs in a process costing system
The flow of costs in the process costing system is similar to in a job-costing system, but let’s review with our Ultimate Planner example:
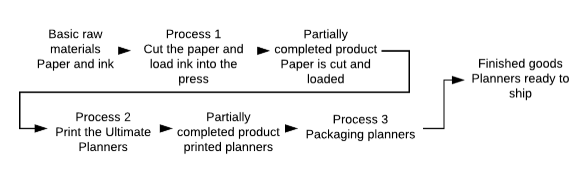
In the process planning we will cost by process. Process 1 involved preparing the raw materials for printing, process 2 is the actual printing, and process 3 is packaging the planners to be moved to finished goods inventory. Costing is simpler in this system because rather than having to prepare a costing sheet for many products, we only need to do costing for three departments or processes.
We start with the basic inputs:
- Raw materials
- Wages
- Manufacturing overhead
Manufacturing overhead will be estimated, just as in the job costing method, but will need to be recorded as incurred. The clearing account will be used to accumulate the actual costs, and a reconciliation will be done at the end of each period.
A processing department is a unit where work is performed on a product and where materials, labor or overhead are added to the product. In the case of our planner, we first add the raw materials, then we add labor to process the raw materials, next conclude with additional labor to package the finished product to prepare it for shipment. These will be the three processes used for costing. Each business will have different processing departments, depending on the product they are making.
Each of these processing departments will be a work-in-process center. So a job costing system may have only one work-in-process, while a process costing system will have several. In the Ultimate Planner example, there will be three WIP accounts.
Raw materials, labor and overhead can be added during any process. So the costs in Process 2 will include everything happening in that process, plus the costs that are attached to the partially completed product transferred in from Process 1. These are called transferred-in costs.
Practice Questions
Here’s another example: a company manufactures 16” chocolate chip cookies similar to those in the cookie shops in the malls. The company’s factory has three departments: (1) Mixing, (2) Baking, and (3) Packaging. The products move through these departments in order: Mixing first, Baking next, and Packaging last. The process occurs on a FIFO (first in, first out) basis where the first batch started is the first one to be completed. The batch started behind the first batch is the next to be completed, and so forth. Each time the Mixing Department adds more ingredients, a new batch is introduced into the overall production line.
Process costing involves recording product costs for each manufacturing department (or process) as the product moves through. Each department has its own Work in Process and Factory Overhead accounts that include the department names, as follows:
Department | Work in Process account | Factory Overhead account |
Mixing | Work in Process – Mixing | Factory Overhead – Mixing |
Baking | Work in Process – Baking | Factory Overhead – Baking |
Packaging | Work in Process – Packaging | Factory Overhead – Packaging |
The batch moves from one department to the next. Materials, labor, and factory overhead costs are added in each department. The sum of the departmental work in process costs is the total cost of the batch that is transferred to Finished Goods.
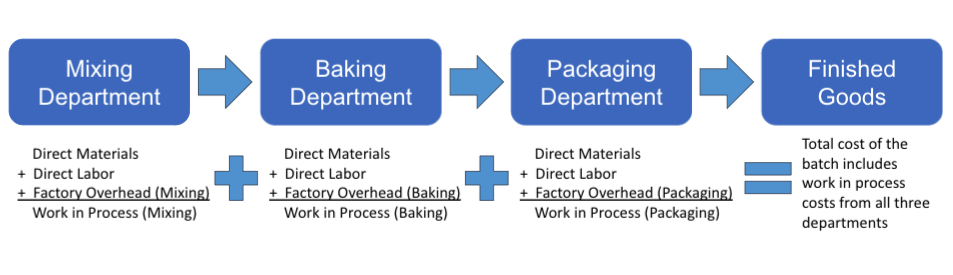
The diagram above shows the cost flows in a process cost system that processes the products in a specified sequential order. That is, the production and processing of products begin in the Mixing Department. From the Mixing Department, products go to the Baking Department. From the Baking Department, products go to the Packing Department. Each Department inputs direct materials and further processes the products. Then the Packaging Department transfers the products to Finished Goods Inventory.