Learning Outcomes
- Define operations management
- Explain the role of the operations manager
It’s one thing to be in charge of getting Thanksgiving dinner on the table, but it’s another to manage a complex manufacturing process. Before we explore what’s involved in such an undertaking, let’s begin our study of processes and operations by defining some key terms you will use throughout this module.
Production, the creation of products and services, is an essential function in every firm. Production turns inputs, such as natural resources, raw materials, human resources, and capital, into outputs, which are products and services. This process is shown below. Managing this conversion process is the role of operations management.
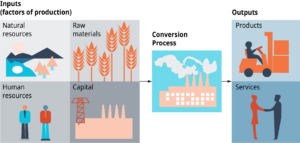
Production Process for Products and Services (Attribution: Copyright Rice University, OpenStax, under CC BY 4.0 license.)
Practice Question
Operations managers, the people charged with managing and supervising the conversion process, play a vital role in today’s firm. They control about three-fourths of a firm’s assets, including inventories, wages, and benefits. They also work closely with other major divisions of the firm, such as marketing, finance, accounting, and human resources, to ensure that the firm produces its goods profitably and satisfies its customers. Marketing personnel help them decide which products to make or which services to offer. Accounting and human resources help them face the challenge of combining people and resources to produce high-quality goods on time and at reasonable cost. They are involved in the development and design of goods and determine what production processes will be most effective.
Production and operations management involve three main types of decisions, typically made at three different stages:
- Production planning. The first decisions facing operations managers come at the planning stage. At this stage, managers decide where, when, and how production will occur. They determine site locations and obtain the necessary resources.
- Production control. At this stage, the decision-making process focuses on controlling quality and costs, scheduling, and the actual day-to-day operations of running a factory or service facility.
- Improving production and operations. The final stage of operations management focuses on developing more efficient methods of producing the firm’s goods or services.
PRactice Question
Candela Citations
- Practice Questions. Authored by: Robert Danielson. Provided by: Lumen Learning. License: CC BY: Attribution
- Production and Operations Management - An Overview. Provided by: OpenStax. Located at: http://cnx.org/contents/4e09771f-a8aa-40ce-9063-aa58cc24e77f@8.5. License: CC BY: Attribution. License Terms: Download for free at http://cnx.org/contents/4e09771f-a8aa-40ce-9063-aa58cc24e77f@8.5