Learning Outcomes
- Describe the flow of costs for a manufacturing company
A manufacturing company has three general categories of inventory:
- Raw materials
- Work in process
- Finished Goods
Raw materials consist of both direct materials and indirect materials.
Work in process (WIP) are products that are not yet ready for sale.
Finished goods are products that are completely done and ready to go out the door.
Let’s look at an example.
ClockCo makes clocks. The gears and casings they buy from their supplier are the direct raw materials the employees will convert into clocks. Each clock gets a certain number of gears and one case. However, the paint the company purchases in 5-gallon buckets are spread out over a number of clocks and can’t be traced to any one particular clock (cost object), and paint is treated as indirect materials and therefore is part of manufacturing overhead (MOH).
Remember that manufacturing overhead is anything that can’t be directly assigned to a specific product.
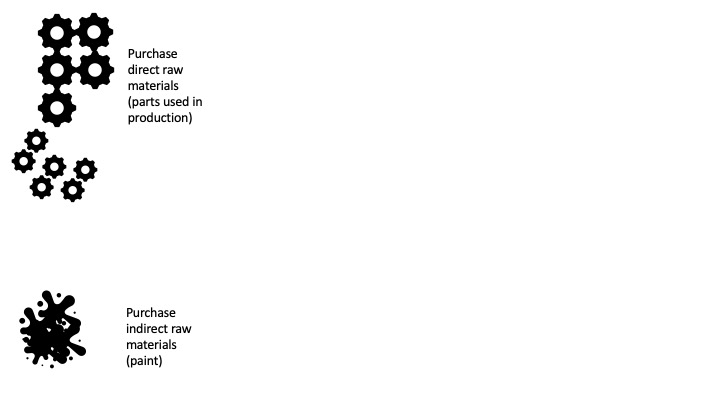
Assuming ClockCo has no clocks in production yet, the company only has raw materials inventory. However, as the company moves gears into the production line and starts painting, raw materials inventory is reduced, and a new category of inventory called Work in Process arises.
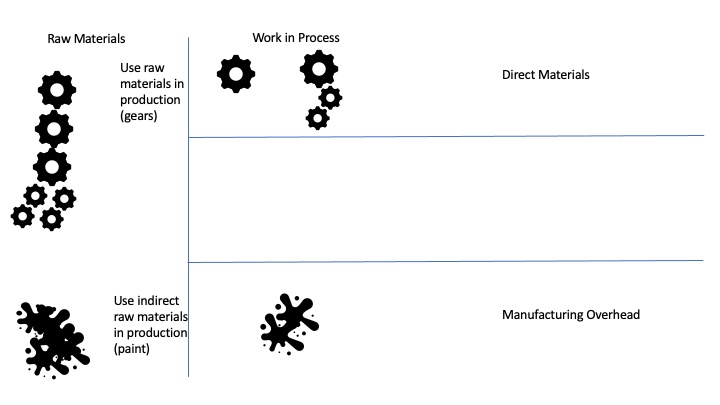
Work in process also includes direct and indirect labor and other manufacturing overhead costs.
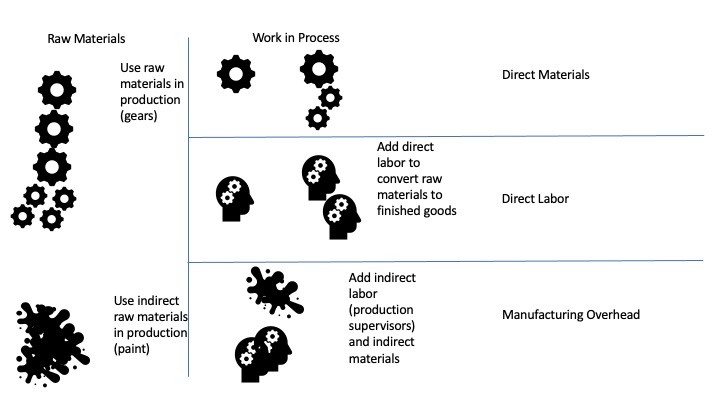
As a clock is finished, all of the costs associated with building that clock (prime and conversion costs) are transferred to an inventory account called Finished Goods.
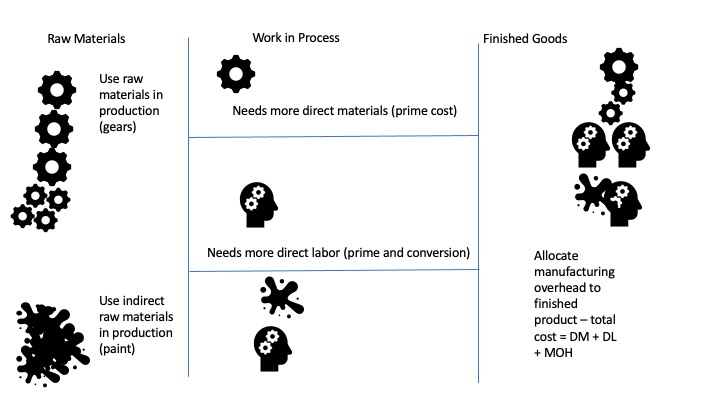
Cost of goods manufactured is the total of all the raw materials, direct labor, and allocated manufacturing overhead used during the period to create completed products.
Determine transfers from Raw Materials to Work in Process and from Work in Process to Finished Goods inventory accounts according to this formula:
Beginning inventory balance + additions during the month – ending inventory balance = transfers out.
Raw Materials
For instance, assume ABC Manufacturing Company had $12,000 in raw materials at the beginning of July, determined by taking a physical count at the end of June and assigning costs to the items.
During the month, the company bought $160,000 of raw materials. We’ll assume for this example that all raw materials are direct materials, just to simplify the calculations.
Raw materials available for use during the month were $172,000 (12,000+160,000). At the end of the month, a physical count established that the cost of ending raw materials inventory was $5,000. Therefore, raw materials used up during the month (transferred to Work in Process) was $167,000 (172,000 – 5,000).
Description | Amount |
---|---|
Direct Materials Used: | |
Beginning Direct Materials | $ 12,000 |
Purchases of Direct Materials (including Freight In) | 160,000 |
Direct Materials Available for Use | Single Line172,000 |
Ending Direct Materials | $ (5,000) |
Direct Materials Used | Single Line$ 167,000 |
Work in Process
Assume ABC incurred $88,000 in direct labor and $90,000 in manufacturing overhead. Total costs incurred in the manufacturing process would then be $345,000 as shown below.
Description | Amount | Total |
---|---|---|
Direct Materials Used | $ 167,000 | |
Direct Labor | $ 88,000 | |
Manufacturing Overhead | $ 90,000 | |
Total Manufacturing Costs Incurred during the Year | Single Line | $ 345,000 |
The total manufacturing costs we need to account for include the $345,000 costs in July, plus work in process from June. Let’s assume that amount was $66,000. Most likely, those products were finished in July (although that’s not necessarily true). In any case, for July, we have the $66,000 in work in process carried forward plus $345,000 in new costs for a total of $411,000.
Description | Amount | Total |
---|---|---|
Beginning Work-in-Process Inventory | $ 66,000 | |
Direct Materials Used: | ||
Beginning Direct Materials | $ 12,000 | |
Purchases of Direct Materials (including Freight In) | 160,000 | |
Direct Materials Available for Use | Single Line172,000 | |
Ending Direct Materials | $ (5,000) | |
Direct Materials Used | Single Line$ 167,000 | |
Direct Labor | $ 88,000 | |
Manufacturing Overhead | $ 90,000 | |
Total Manufacturing Costs Incurred during the Year | Single Line | $ 345,000 |
Total Manufacturing Costs to Account For | Single Line$ 411,000 |
It’s likely at this point that, based on a physical count, we know either:
- Cost of ending work in process, or
- Cost of goods manufactured (completed and ready to be sold).
In this managerial accounting course, you’ll be learning how to calculate those amounts using either job costing or process costing, but for now, let’s assume we know the cost of goods manufactured is $395,000. For instance, we could have calculated that our cost per unit, taking into account direct materials, direct labor, and allocated manufacturing overhead, is $395, and we manufacture 1,000 completed units. Therefore, the cost of items sitting in work in process—started but not yet completed—is $16,000 (411,000 – 395,000).
Now we can complete the schedule of cost of goods manufactured.
Description | Amount | Total |
---|---|---|
Beginning Work-in-Process Inventory | $ 66,000 | |
Direct Materials Used: | ||
Beginning Direct Materials | $ 12,000 | |
Purchases of Direct Materials (including Freight In) | 160,000 | |
Direct Materials Available for Use | Single Line172,000 | |
Ending Direct Materials | $ (5,000) | |
Direct Materials Used | Single Line$ 167,000 | |
Direct Labor | $ 88,000 | |
Manufacturing Overhead | $ 90,000 | |
Total Manufacturing Costs Incurred during the Year | Single Line | $ 345,000 |
Total Manufacturing Costs to Account For | Single Line$ 411,000 | |
Ending Work-in-Process Inventory | (16,000) | |
Cost of Goods Manufactured | Single Line$ 395,000Double line |
Here is a video review of how to complete a schedule of cost of goods manufactured.
You can view the transcript for “How to Prepare a Cost of Goods Manufactured Statement (Cost Accounting Tutorial #24)” here (opens in new window).
In the next section, we’ll see how the cost of goods sold flows to the income statement, but first, let’s review cost of goods manufactured.
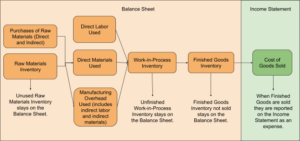
Description | Equation |
---|---|
Direct Materials Used | Beginning Raw Materials Inventory + Raw Material Purchases – Ending Raw Materials Inventory – Indirect Materials Used |
Total Manufacturing Cost | Direct Materials + Direct Labor + Overhead applied |
Cost of Goods Manufactured | Total Manufacturing Cost (Direct Materials + Direct Labor + Overhead applied) + Beginning Work In Process Inventory – Ending Work in Process Inventory |
Now, check your understanding of the flow of costs in a manufacturing environment: