Learning Objectives
- Explain how labor evolved from the “putting-out system” to unskilled wage labor during the early Industrial Revolution
- Describe industrialization’s impact on the nature of work
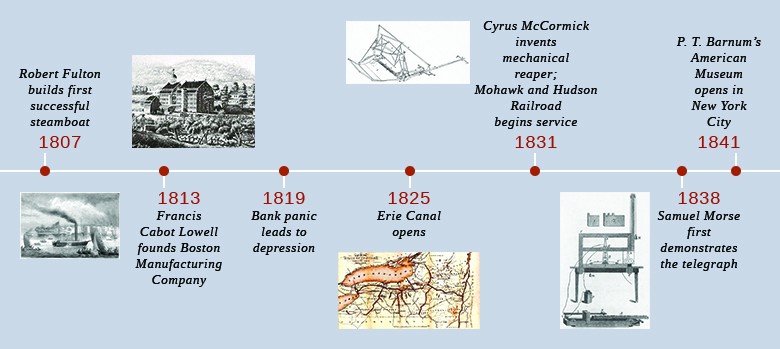
Figure 1. Major milestones in industrialization (credit “1807 photo”: Project Gutenberg Archives).
Northern industrialization expanded rapidly following the War of 1812. Industrialized manufacturing began in New England, where wealthy merchants built water-powered textile mills (and centralized company towns to support them) along the rivers of the Northeast. These mills introduced new modes of production centralized in the confines of the mill itself. Production now relied on complex machinery powered by water, and later steam. In addition to the mechanization and concentration of work in the mills, specialized, repetitive tasks assigned to wage laborers replaced earlier modes of skilled handicraft production, which was done by artisans in their home. The operation of these mills irrevocably changed the nature of work by deskilling tasks and breaking down the process of production to its most basic elements. In return for their labor, the workers received hourly wages and sometimes a place to live in one of the mill town boarding houses. Many of these original unskilled laborers were young women from rural New England farming families. From its origin in New England, industrial manufacturing soon spread to other regions of the United States.
From Artisans to Wage Workers
During the seventeenth and eighteenth centuries, artisans—skilled, experienced craft workers—produced goods by hand. The production of shoes provides a good example. In colonial times, people bought their shoes from master shoemakers, who achieved their status by living and working as apprentices under the rule of an older master artisan. After completing an apprenticeship, a young artisan would work as a journeyman (a skilled worker without his own shop). After sufficient time as a journeyman, a shoemaker could at last set up his own shop as a master artisan. People came to the shop, usually attached to the back of the master artisan’s house, and there the shoemaker measured their feet in order to cut and stitch together an individualized product for each customer.
In the late eighteenth and early nineteenth century, merchants in the Northeast and elsewhere turned their attention as never before to the benefits of using unskilled wage labor to make a greater profit by reducing labor costs. They used the putting-out system, which the British had employed at the beginning of their own Industrial Revolution, whereby they hired farming families to perform specific tasks in the production process for a set wage. This system of “piece work” divided much of production into discrete steps performed by different workers. In this new system, merchants or investors sent or “put-out” raw materials for goods, which individuals or families would then begin to make at home. These independent laborers then turned over the partially finished goods to another laborer to finish. In the case of shoes, for instance, American merchants hired one group of workers to cut soles into standardized sizes. A different group of families cut pieces of leather for the uppers, while still another was employed to stitch the standardized parts together.
This process proved attractive because it reduced production costs. The families who participated in the putting-out system were not skilled artisans. They had not spent years learning and perfecting their craft and did not have ambitious journeymen to pay. Therefore, they could not demand—and did not receive—high wages. Most of the year they tended fields and orchards, ate the food that they produced, and sold the surplus. Putting-out work provided a welcome source of extra income for New England farm families, who were beginning to see their profits dwindle due to competition from new Midwestern farms with higher-yield land.
Much of this part-time production was done under contract to merchants. Some farming families engaged in shoemaking (or shoe assemblage), as noted above. Many made brooms, plaited hats from straw or palm leaves (which merchants imported from Cuba and the West Indies), crafted furniture, made pottery, or wove baskets. Some, especially those who lived in Connecticut, made parts for clocks. The most common part-time occupation, however, was the manufacture of textiles. Farm women spun woolen thread and wove fabric. They also wove blankets, made rugs, and knit stockings. All this manufacturing took place in their homes, giving families control over the pace of their labor. Their domestic productivity increased the quantity of goods available for sale in country towns and nearby cities and drove further advances in manufacturing.
Try It
American Manufacturing and Changes in Labor
As early as the 1790s, merchants in New England began experimenting with machines to replace the “putting-out system.” To effect this transition, merchants and factory owners relied on British technological knowledge to build the machines they needed. In 1789, a textile mill in Pawtucket, Rhode Island contracted twenty-one-year-old British immigrant Samuel Slater to build a yarn-spinning machine and carding machine. Slater had apprenticed in an English mill and was familiar with the design of their machinery. American “industrial espionage” began to pay off in 1813 when Francis Cabot Lowell, a merchant from Boston, returned from a two-year trip to Britain. Lowell was desperate to find a way to allow the U.S. to keep up with England’s textile production, but British law prohibited the sale of manufacturing equipment to Americans. He had committed the design of the British power loom to memory during his trip so that he could smuggle England’s industrial know-how into Massachusetts. Lowell hired a machinist named Paul Moody to recreate the powered looms and in 1814 he opened the Boston Manufacturing Company, which used the Charles River to power the first integrated textile mill, a setup where all production steps from handling raw materials to presenting finished goods was combined under one roof.
Lowell’s contribution to American industrialism was not only technological but also organizational, helping to streamline and centralize the American manufacturing process. His new approach, the Waltham-Lowell System, created the textile mill that defined antebellum New England and American industrialism. This modern manufacturing process was fully realized in the planned mill town of Lowell, Massachusetts in 1821, four years after Francis Lowell died. Powered by the Merrimack River and operated by local farm girls, the mills of Lowell centralized the process of textile manufacturing under one roof. The modern American factory was born. Soon, ten thousand employees worked in Lowell alone. Sarah Rice, who worked at the nearby Millbury factory, found it “a noisy place” that was “more confined than I like to be.” Working conditions were harsh for the “mill girls” who operated the factories from sun-up to sun-down. One worker complained that “a large class of females are, and have been, destined to a state of servitude.” These women organized strikes and lobbied for better hours, but the appeal of wage labor was high. As another worker noted, “very many Ladies…have given up millinery, dressmaking & school keeping for work in the mill.” With a large supply of eager workers, Lowell’s vision brought a rush of capital and entrepreneurs into New England, resulting in the first manufacturing boom in the new republic.
The Changing Nature of Work
The market revolution shook other industries as well. Craftsmen began to understand that new markets increased the demand for their products. Some shoemakers, for instance, abandoned the traditional method of producing custom-built shoes at their home workshop and instead began producing larger quantities of shoes in ready-made sizes to be shipped to urban centers. Manufacturers who wanted increased production abandoned the old personal approach of relying upon a single live-in apprentice for labor and instead hired unskilled wage laborers. These workers did not have to be trained in all aspects of making shoes but could simply be assigned a single repeatable aspect of the task. Factories slowly replaced shops. The old paternalistic apprentice system, which involved long-term obligations between apprentice and master, gave way to a more impersonal and more flexible labor system in which unskilled laborers could be hired and fired as the market dictated. A writer in the New York Observer in 1826 complained that “The master no longer lives among his apprentices [and] watches over their moral as well as mechanical improvement.” Such sentiments were an early indicator that the new labor arrangements were transforming both social relations and more impersonal economic hierarchies.
Masters-turned-employers now not only had fewer obligations to their workers but also less personal attachment. They no longer shared the bonds of their trade but were categorized into new class-based relationships: employers and employees, bosses and workers, capitalists and laborers. On the other hand, workers were freed from the long-term obligations of apprenticeship and the legal subjugation of indentured servitude. They could—theoretically—work when and where they wanted. When men or women made an agreement with an employer to work for wages, they were “left free to apportion among themselves their respective shares, untrammeled…by unwise laws,” as Reverend Alonzo Potter rosily proclaimed in 1840. But while the new labor system was celebrated throughout the northern United States by the captains of industry as “free labor,” it was simultaneously lamented by the growing class of powerless laborers who had no recourse against their employers to improve their conditions or their wages.
As the northern United States rushed headlong toward commercialization and an early capitalist economy, many Americans grew uneasy about the growing gap between wealthy businessmen and impoverished wage laborers. Elites like Daniel Webster defended their wealth and privilege by insisting that all workers could achieve “a career of usefulness and enterprise” if they were “industrious and sober,” but labor activist Seth Luther countered that capitalism created “a cruel system of extraction on the bodies and minds of the producing classes…for no other object than to enable the ‘rich’ to ‘take care of themselves’ while the poor must work or starve.”
Americans embarked upon their industrial revolution with the expectation that all men could start their careers as humble wage workers but eventually participate in property ownership and financial stability if they only worked hard enough. Wage work had traditionally been looked down upon as a state of dependence, suitable only as a temporary waypoint for young men without resources on their path toward the economic success necessary to comfortably support a middle-class family. Children’s magazines – such as Juvenile Miscellany and Parley’s Magazine – glorified the prospect of moving up the economic ladder. This “free labor ideology,” where hard work, thrift and a suitably aspirational orientation meant personal advancement, had a darker side too, as mobile workers seeking opportunities would move to the same cities only to face reduced prospects and unenployment due to the sudden oversupply of labor.
The new commercial economy often failed in its promise of social mobility. Depressions and downturns might destroy businesses and reduce their owners to wage work, but even in times of prosperity, unskilled workers perpetually lacked economic security and therefore had to depend upon supplemental income from their wives and young children. This combination of low wages, job competition, deskilling, economic uncertainty, and a lack of workers’ rights led to such atrocities as widespread child labor and crowded urban centers with poor sanitation and unsafe living conditions. With the rise of industrialization and cramped living quarters also came a rise in diseases like cholera, typhoid, and tuberculosis. Workers poured into cities looking for jobs and were often housed in crowded tenement buildings with no running water and entire families living in a single room. In New York City, the death rate rose from 21 in 1000 to 37 in 1000 between 1810 and 1837, an increase of almost 80% in less than 50 years.[1]
Try It
Glossary
artisan: a skilled, experienced worker who produces specialized goods by hand
deskilling: breaking an artisanal production process into smaller steps that unskilled workers can perform
integrated textile mill: a manufacturing operation wherein all steps, from processing raw cotton to the finished textile product, are completed under one roof
putting-out system: a labor system whereby a merchant hired different families to perform specific tasks in a production process
Candela Citations
- Modification, adaptation, and original content. Authored by: Lillian Wills for Lumen Learning. Provided by: Lumen Learning. License: CC BY-SA: Attribution-ShareAlike
- American Yawp. Located at: http://www.americanyawp.com/index.html. Project: American Yawp. License: CC BY-SA: Attribution-ShareAlike
- Early Industrialization in the Northeast. Provided by: OpenStax. Located at: https://openstax.org/books/us-history/pages/9-1-early-industrialization-in-the-northeast. License: CC BY-SA: Attribution-ShareAlike. License Terms: Access for free at https://openstax.org/books/us-history/pages/1-introduction
- Boott cotton mill looms. Authored by: Jlpapple. Provided by: Wikimedia Commons. Located at: https://commons.wikimedia.org/wiki/File:Boott_cotton_mill_looms.jpg. License: CC BY: Attribution
- New England factory life -- 'Bell-time.' (Boston Public Library). Authored by: Winslow Homer / BPL. Provided by: Wikimedia Commons. Located at: https://commons.wikimedia.org/wiki/File:New_England_factory_life_--_%27Bell-time.%27_%28Boston_Public_Library%29.jpg. License: Public Domain: No Known Copyright
- Richard H. Shryock, "The Early American Public Health Movement," The American Journal of Public Health, Vol. 27, No. 10 (Oct. 1937): 966, https://ajph.aphapublications.org/doi/pdf/10.2105/AJPH.27.10.965. ↵