Outsourcing and Quality
PowerSki’s Web site states that “PowerSki International has been founded to bring a new watercraft, the PowerSki Jetboard, and the engine technology behind it, to market.”[1] That goal was reached in May 2003, when the firm emerged from a lengthy design period. Having already garnered praise for its innovative product, PowerSki was ready to begin mass-producing Jetboards. At this juncture, the management team made a strategic decision that’s not uncommon in manufacturing today.
Rather than producing Jetboards in-house, they opted for outsourcing: having outside vendors manufacture the engines, fiberglass hulls, and associated parts. Assembly of the final product took place in a manufacturing facility owned by All American Power Sports in Moses Lake, Washington. This decision does not mean that the company relinquished control over quality; in fact, every component that goes into the PowerSki Jetboard is manufactured to exact specifications set by PowerSki.
One advantage of outsourcing its production function is that the management team can thereby devote its attention to refining its product design and designing future products. However, as processes or pieces of a process are outsourced companies have legitimate concerns about quality standards being met and maintained at the outsourced location. The decision whether or not to outsource often comes down to identifying organizations that can meet and maintain the standards set by the company and the customer.
Outsourcing in the Manufacturing Sector
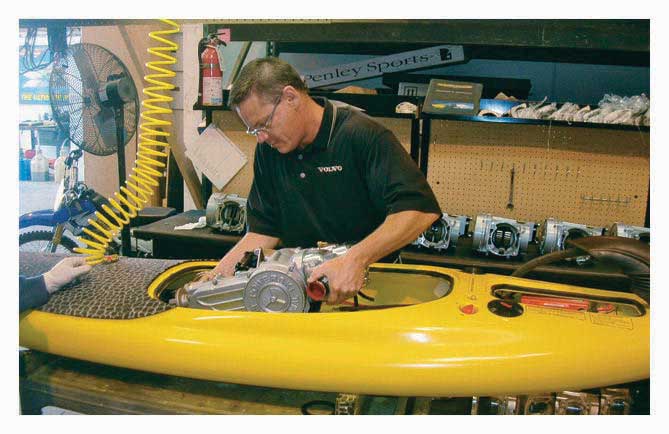
Figure 1. Outsourcing the production of its engines, hulls, and other components enables PowerSki to reduce the cost of producing each Jetboard through manufacturing efficiencies and lower labor costs. All components that go into the Jetboard are made to PowerSki’s specifications and are inspected upon arrival to ensure that they meet the company’s high-quality standards.
Understandably, outsourcing is becoming an increasingly popular option among manufacturers. For one thing, few companies have either the expertise or the inclination to produce everything needed to make a product. Today, more firms, like PowerSki, want to specialize in the processes that they perform best—and outsource the rest. Like PowerSki, they also want to take advantage of outsourcing by linking up with suppliers located in regions with lower labor costs.
Outsourcing in the Service Sector
Outsourcing is by no means limited to the manufacturing sector. Service companies also outsource many of their noncore functions. Your school, for instance, probably outsources such functions as food services, maintenance, bookstore sales, printing, groundskeeping, security, information-technology (IT) support, and even residence operations.
KEY TAKEAWAYS
- Today, companies that compete in both the manufacturing and service sectors must deliver quality goods and services that satisfy customers’ needs. Many companies achieve this goal by adhering to principles of total quality management (TQM).
- Companies using a TQM approach focus on customer satisfaction, engage all members of the organization in quality efforts, and strive for continuous improvement in the design, production, and delivery of goods and services. They also benchmark other companies to find ways to improve their own performance.
- To identify areas for improvement, companies can use a technique called statistical process control (SPC), which monitors quality by testing to see whether a sample of output is being made to predetermined specifications.
- The Deming award is given by Japan to companies doing business in Japan for high-quality standards. Similarly, the Baldrige National Quality Award is given to U.S. companies and individuals for their contribution to quality.
- Six Sigma identifies specialists within the organization and assigns titles like Master Black Belt. Each quality project must evaluate the cost of quality to gain approval.
- The International Standards Institute devises guidelines for establishing practices. The ISO 9000 group are guidelines for establishing practices that are likely to create quality products.
- The cost of quality has two parts: the cost of prevention and the cost of failure. The cost of prevention includes costs to establish quality practices and the costs to verify them. The cost of failure includes internal costs before the product is sold, such as waste and fixing products, while external costs include those that occur after the product is sold, such as returns and lawsuits.
- Another cost-saving approach is outsourcing—having outside vendors manufacture components or even entire products or provide services, such as information-technology support or service center operations.
- Outsourcing is an appealing option for companies without the expertise in producing everything needed to make a product or those that want to take advantage of low labor costs in developing countries.
Check Your Understanding
Answer the question(s) below to see how well you understand the topics covered in this section. This short quiz does not count toward your grade in the class, and you can retake it an unlimited number of times.
Use this quiz to check your understanding and decide whether to (1) study the previous section further or (2) move on to the next section.
Candela Citations
- Revision and adaptation. Authored by: Linda Williams and Lumen Learning. Provided by: Tidewater Community College. License: CC BY-NC-SA: Attribution-NonCommercial-ShareAlike
- An Introduction to Business. Authored by: Anonymous. Provided by: Anonymous. Located at: http://2012books.lardbucket.org/books/an-introduction-to-business-v2.0/s15-07-producing-for-quality.html. License: CC BY-NC-SA: Attribution-NonCommercial-ShareAlike
- “About PowerSki International,” PowerSki, (accessed November 3, 2011). ↵