Learning Outcomes
- Estimate expected labor costs
The chief financial officer is not happy. Labor is at an all time high, and something needs to give to be able to continue pricing your product competitively in a tight market. You go to your production manager to discuss options for reducing labor, but it seems as if she has the process down, and she can’t see a way to reduce the time per pair of shoes to anything lower than it is. Putting on your thinking caps, you work together to go through the process step-by-step, to see if there are ways to decrease the labor time, automate steps or have a lower wage employee complete certain steps. But then you get the news, that your best guy is leaving. Are you ready to take on this task of replacing him?
Take a look at this chart again and then watch this video for a review of variance analysis.
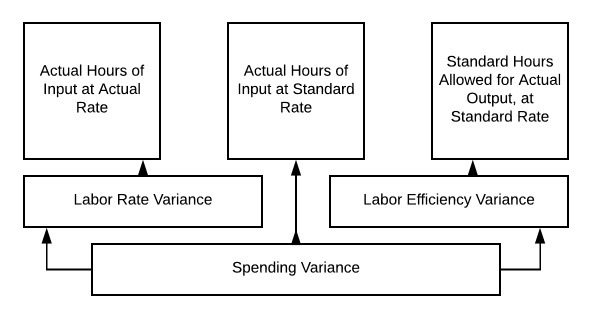
Hupana Running Company has a great direct labor budget prepared by their experienced production manager, Mary. She has production hours down like a well oiled machine. Once she got the sales and production numbers, she prepared her direct labor budget:
Q1 | Q2 | Q3 | Q4 | Total | |
---|---|---|---|---|---|
Required Production in Pairs | 450 | 500 | 500 | 600 | 2050 |
Direct labor hours-pair | 0.5 | 0.5 | 0.5 | 0.5 | 0.5 |
Total direct labor hours needed | 225 | 250 | 250 | 300 | 1025 |
Direct labor cost per hour | $20 | $20 | $20 | $20 | $20 |
Total direct labor cost | $4,500 | $5,000 | $5,000 | $6,000 | $20,500 |
Mary has a great bunch of people working for her and is confident that they can stay on task from a labor perspective. But then she gets the fateful news. Her best machine operator is leaving for another opportunity. She is going to need to replace him, and that won’t be an easy task.
Mary interviews a few people, and settles on hiring Jake. He has some similar experience, but the labor market is tight, so she needs to pay him $22 per hour instead of $20. Bringing him on at that rate, requires raises all around, so now, the direct labor cost per hour is $22, an increase of $2 per hour.
How will that affect the direct labor budget? This could cause a couple of things to happen.
- Your hourly labor rate will go up since you are paying Jake more than you were paying the previous operator.
- You may see a production slow down as Jake learns his new job.
- You could see a lower employee engagement or satisfaction rate, with the departure of a long-term employee.
How do you handle all of these situations?
Practice Questions