What you will learn to do: allocate manufacturing overhead using Activity-Based Costing (ABC)
The simplest method for estimating factory overhead is to use the same predetermined rate in all departments, for all activities and for all products in a manufacturing facility. Two amounts must be estimated for the calculation, as follows:
Total budgeted factory overhead
Total budgeted activity base (such as direct labor hours, machine hours, etc.)
The single factory overhead rate is a very loose estimate because it relies on one fixed dollar amount to assign factory overhead costs across the many facets, various segments, and different activities involved in the manufacturing process. It is unlikely that one rate can capture all the diversity of what goes on in a factory with reliable precision.
Departmental rates are more precise than a single, organization-wide rate, but another option is Activity-Based Costing (ABC).
Activity-based costing (ABC) is a more specific and more accurate way of assigning factory overhead to manufactured goods versus using a single factory or multiple departmental rates. An activity is a unit of work that consumes resources when performed by a company. A cost object (in the case of manufacturing, the item produced) is the target of the activity. Common examples of cost objects include products, jobs, services, projects, clients, patients, customers, and contracts.
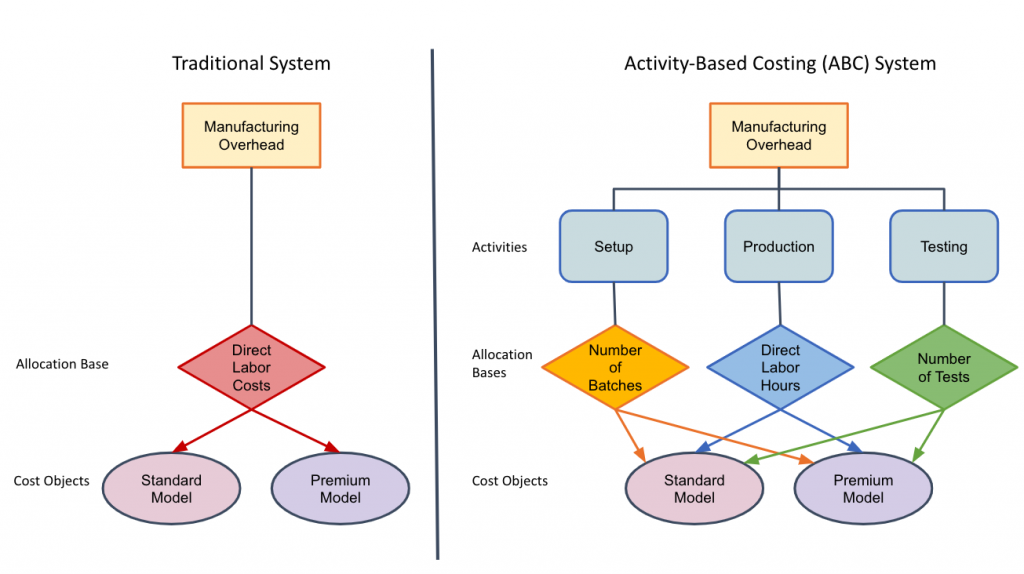
The steps for allocating costs by activity are:
- Identify all the activities required to create the product. These will be the cost pools. Each pool includes all the individual costs related to an activity.
- Using the accounting information system, accumulate the total overhead for each cost pool.
- Assign each cost pool activity cost drivers, such as hours, units, number of tests, or number of documents processed.
- Calculate the activity rate by dividing the total overhead in each cost pool by the total of the cost driver.
- Just like allocating based on a single rate or departmental rates, multiply the rate by the number of cost drivers for each product.
When you are done with this section, you will be able to:
- Identify activities and estimate total indirect costs for each
- Identify cost drivers and compute allocation rates
- Allocate costs to cost objects using Activity Based Costing
Learning Activities
The learning activities for this section include the following:
- Reading: Defining Activities
- Self Check: Defining Activities
- Reading: Identifying Cost Drivers
- Self Check: Identifying Cost Drivers
- Reading: Reading: Allocating Overhead using ABC
- Self Check: Allocating Overhead using ABC